Gas Burner Systems for Mould and Die Heating in Forging Applications
- Sean Davies
- 7 days ago
- 2 min read
Updated: 4 days ago
Metal forging relies on intense heat and force to shape components into their desired form. An often-overlooked aspect of this process is the precise heating of the moulds and dies themselves. In forging operations—whether open-die, closed-die, or precision forging—uniform die temperature is critical. Uneven or insufficient heating can lead to poor material flow, thermal cracking, and dimensional inconsistencies in the final product.
Gas Burners for Mould and Die heating in forging
Rapidflame specialises in gas burner systems engineered for industrial applications like these. Our solutions are designed to deliver consistent, controllable heating of dies and moulds in forging setups—whether stand-alone or integrated into automated production lines.
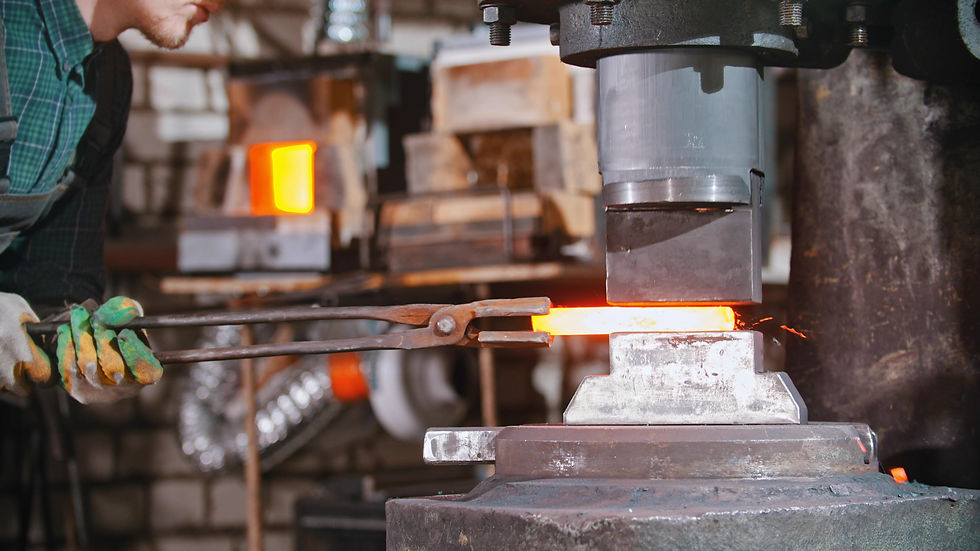
Why Uniform Die Heating Matters
During metal forging, moulds and dies act as thermal sinks. If not adequately preheated, they can extract heat from the workpiece too quickly, causing defects. Properly heated dies allow better material flow, reduce internal stresses, and ensure dimensional accuracy.
In high-throughput environments, inconsistent heating between cycles can also cause productivity losses. Using a reliable gas burner system for die preheating ensures that each forging cycle starts under optimal thermal conditions.
Rapidflame’s Heating Systems for Forging Dies
Our industrial burner systems provide:
- Fast and even heat-up of large die surfaces
- Controlled flame impingement for minimal thermal gradient
- Integration with automated process controls for repeatability
- Compatibility with temperature monitoring systems
Applications in Metal Forging
Common use cases include:
- Preheating closed-die forging tools before production runs
- Maintaining steady temperature during long forging shifts
- Heating multi-part mould assemblies evenly
- Rapid re-heating of dies between component batches
These applications are particularly relevant in industries producing automotive components, aerospace fasteners, and large industrial hardware.
Talk to Our Technical Team
We can advise on burner configurations tailored to your forging equipment and production goals. Whether you require stand-alone combustion systems or fully integrated heating control system, we can help.
Contact us directly to find out how our systems can help with your metals production
Frequently Asked Questions (FAQs)
What temperature should forging dies be preheated to?
Typical die preheat temperatures range from 150°C to 400°C depending on the alloy and forging process. Rapidflame systems can be adjusted to meet these requirements safely.
Can Rapidflame burner systems be automated?
Yes. Rapidflame systems can be integrated with temperature sensors, PLCs, and automated cycle controls for consistent, repeatable heating.
Why use gas burners instead of electric heaters for die heating?
Gas burners provide faster ramp-up and better controllability in heavy-duty applications. They also allow higher energy densities, which is useful for large or complex dies.
Do you supply burner systems for large moulds used in press forging?
Yes. We supply modular burner systems that can be scaled for large surface areas and heavy dies. Our technical team can help configure the right solution.